What Does the Durability of Vacuum Food Bags Depend On? ZB PACKAGING In-Depth Analysis
- Share
- Issue Time
- Jul 7,2025
Summary
Learn how material quality, sealing technology, storage conditions and manufacturing processes affect the life of vacuum food bags. Trust ZB PACKAGING for quality vacuum packaging solutions.
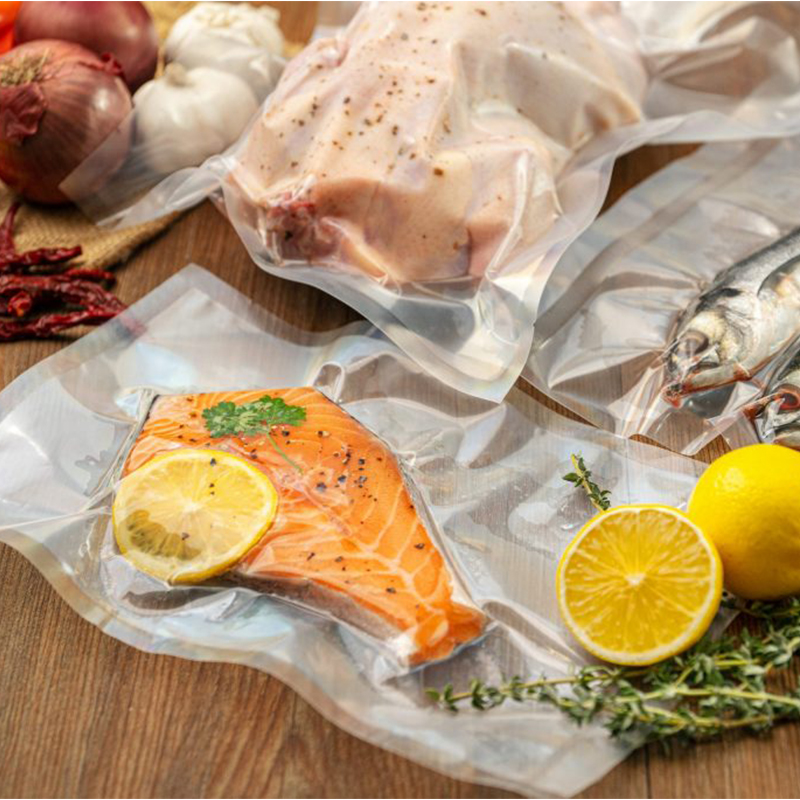
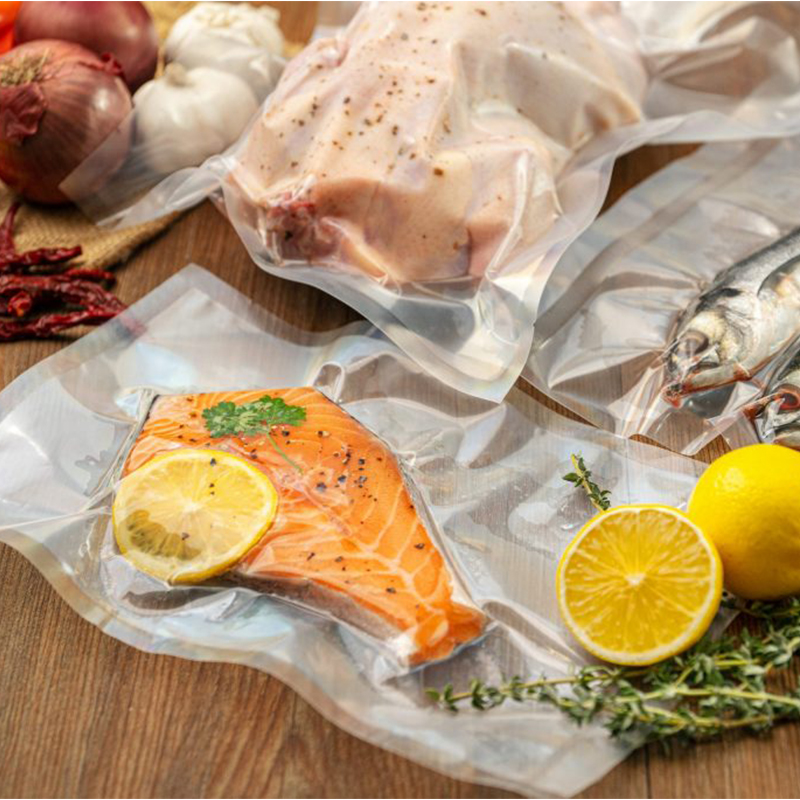
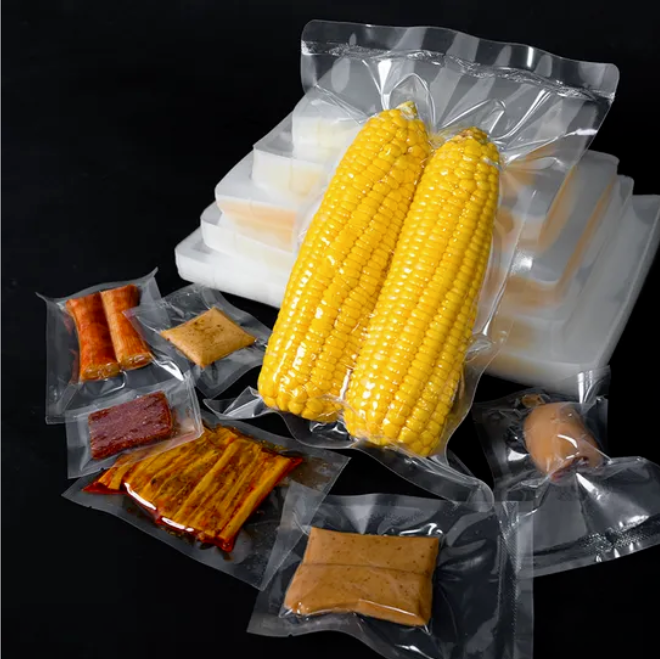
The durability of vacuum food bags is critical to maintaining the freshness, safety and quality of stored food. As a leading supplier of vacuum packaging solutions, ZB PACKAGING is committed to providing high-quality, reliable vacuum bags that meet the highest standards. Understanding the many factors that affect the life of vacuum bags is crucial for manufacturers, food processors and consumers to optimize shelf life and minimize waste.
In this comprehensive exploration, we will analyze the core factors that determine the durability of vacuum food bags, including material composition, manufacturing process, sealing technology, storage conditions and operating specifications. By understanding these factors, stakeholders can significantly improve the performance and service life of vacuum packaging.
1. Material Composition: The Foundation of Vacuum Food Bag Durability
The material of vacuum food bags is the main factor that determines their strength, flexibility, puncture and tear resistance. The most commonly used materials include polyethylene (PE), polyamide (PA or nylon), polypropylene (PP), and barrier films such as ethylene vinyl alcohol (EVOH) and metalized films.
High-Barrier Films Extend Shelf Life
Barrier films are essential to protect food from oxygen, moisture and light, which can accelerate spoilage. EVOH and metallized films have excellent barrier properties and can significantly extend the life of vacuum bags. Laminated structures of these films with polyethylene or polyamide provide enhanced mechanical strength, ensuring that the bags can withstand the stresses during handling and storage.
Material Thickness and Specifications
Thickness (measured in millimeters or microns) directly affects durability. Thicker bags are generally more resistant to punctures, tears and abrasion than thinner bags. However, too much thickness can affect flexibility and increase costs. Choosing the optimal thickness, balancing durability and cost-effectiveness is crucial. At ZB PACKAGING, we recommend a thickness range tailored to the specific application, ensuring maximum protection without wasting material.
Material Flexibility and Resistance
Flexible and durable materials are able to seal tightly and conform to irregularly shaped food products, reducing the risk of leakage. At the same time, the material must be able to resist cracking and embrittlement over a long period of time, especially under temperature fluctuations.
2. Manufacturing Process: Precision and Quality Control
The manufacturing process is critical to the long-term durability of vacuum food bags. High-quality production methods such as lamination, co-extrusion and advanced sealing technologies ensure consistent performance.
Lamination and Co-extrusion
The lamination process bonds multiple layers of different films together to achieve a balance between barrier properties and mechanical strength. Co-extrusion can produce multiple layers of film in a single process, reducing potential weak points and ensuring uniform layer bonding.
Quality Control and Inspection
Strict quality assurance procedures - including visual inspection, leak testing and tensile strength testing - are essential. ZB PACKAGING has invested heavily in advanced inspection equipment to detect even the smallest defects that may affect the durability of the product.
3. Sealing Technology: Ensuring a Strong Barrier
The integrity of the seal is critical to the durability of vacuum packaging. A poor seal can lead to air ingress, moisture penetration, and food spoilage.
Heat Sealing Parameters
Precise control of sealing temperature, pressure and holding time ensures a consistent and airtight seal. Over-sealing can lead to burn-through, weakening the bag, while under-sealing presents a risk of leakage. ZB PACKAGING uses advanced sealers with programmable parameters to ensure optimal results.
Seal Width and Pattern
A wider seal generally provides a stronger barrier. The seal pattern (e.g. full width or intermittent) must be designed to maximize seal strength without compromising flexibility.
Double Seal and Impulse Seal
For high-risk applications, double seal or impulse seal technology provides redundant protection, ensuring durability even under rigorous handling or temperature fluctuations.
4. Storage Conditions: External Factors Affecting Durability
The storage environment of a vacuum bag can significantly affect its long-term performance.
Temperature Stability
Extreme temperatures, both hot and cold, can change material properties. High temperatures can cause the material to soften or seal poorly, while low temperatures can cause the material to become brittle.
Humidity and Moisture Exposure
Excessive humidity can cause condensation inside the package, promote microbial growth and cause material deterioration. Proper storage in a dry, cool environment will maintain the integrity of the vacuum bag.
Light and UV Exposure
Extended exposure to UV rays can weaken some plastics, causing them to become brittle. Using UV-resistant materials or opaque packaging can help reduce this risk.
5. Handling and Usage Practices: Maintaining Durability During Use
Proper handling during manufacturing, shipping and use is essential to maintaining the life of the vacuum bag.
Avoiding Mechanical Damage
Sharp objects, rough handling and rough surfaces can all cause the package to break or tear. Careful handling practices and reinforced areas in the bag design can reduce the risk of damage.
Proper Sealing and Removal
Ensuring proper sealing techniques and gentle removal of the product from the vacuum chamber or sealer can prevent seal failure. ZB PACKAGING provides comprehensive training and guidelines to ensure optimal use.
Temperature during Sealing
Sealing at recommended temperatures prevents weak seals or material deformation. Consistency in sealing conditions improves durability.
ZB PACKAGING Vacuum Food Bag Technology Innovations
At ZB PACKAGING, we use cutting-edge technology to produce vacuum bags with superior durability. Our innovations include:
- Multi-layer barrier films with enhanced resistance to oxygen and moisture.
- Advanced sealing machines for precise control of parameters.
- Customizable bag designs for specific food types and storage needs.
- Environmentally friendly materials that do not compromise performance.
- Strict quality control ensures that every batch meets stringent durability standards.
Conclusion: Interaction of Factors That Determine the Durability of Vacuum Food Bags
The durability of vacuum food bags depends on many factors, including material quality, manufacturing precision, sealing technology, storage environment and operating specifications. ZB PACKAGING ensures that vacuum bags are durable and reliable through strict control of each link, thereby protecting food, extending shelf life and reducing waste.
Investing in high-quality materials, applying advanced manufacturing technologies and following best operating practices are essential to achieve the highest durability. Our commitment to excellence ensures that every vacuum bag printed with the ZB PACKAGING brand provides excellent performance, reliability and value.
Contact ZB PACKAGING today to learn about our range of vacuum packaging solutions and find out how we can help you optimize your food storage and preservation strategy with durable, high-performance vacuum bags.
Retort pouches can be customized a rotogravure printing that creates rich, vibrant designs on the outer layer of the package.
Durable and Puncture-resistant Food Grade Vacuum Packaging Bag